System Upgrade Program
Due to the aging infrastructure in our distribution system, in 2018 the Board and Management developed a 10-year Strategic Plan which includes a priority list for pipe replacement of much of our aging and failing infrastructure.
We have always had a strong gas balancing program which indicates where there may be leaks or failures. A trend was identified where there was a marked increase of leaks on our 50-year-old pipe.
Management worked with our Auditor to show the Board of Directors a business plan for pipe replacement which included cost comparisons using third party contractors vs. the cost of owning the equipment and hiring staff to carry out self-construction for the installation of new pipe. At this time, the Board and Management decided that ownership and control was worth the investment. We decided to finance the equipment purchases in order to balance our cash flow. This meant the purchase of larger equipment had to be new in order for the bank to approve lending.
It was obvious from early on that there were many advantages to owning the equipment and hiring additional staff. Owning the equipment would pay for itself within the first 5 years of the 10-year plan. We purchased the required equipment, then hired one full time and one part time employee to perform the work. We quickly discovered other advantages to having the equipment available full time. We had more control of our schedules and found we could respond to emergencies much faster.
In 2020 we started a replacement program for our RMO facilities (Regulating, Monitoring and Odorization). These facilities are located where we purchase natural gas off of the TransCanada Pipeline system. We replaced Tap 30 (Aspelund Road) with a new facility that is designed to eliminate fugitive emissions including a different design for over pressure protection where we no longer relieve gas to atmosphere. This was important as environmental awareness has become more stringent.
In February 2021, we experienced peak load for an extended period. Our end pressures showed over subscribed pipelines where the draw almost exceeded the ability to deliver gas to the consumer.
Needless to say, we identified some urgent “loop” lines to increase capacity at the downstream consumers on some of our taps. With the application for 3 large grain dryer services, and the emergent loop lines we managed to install more than double the pipe we have installed in previous years. Both through self construction and third party construction.
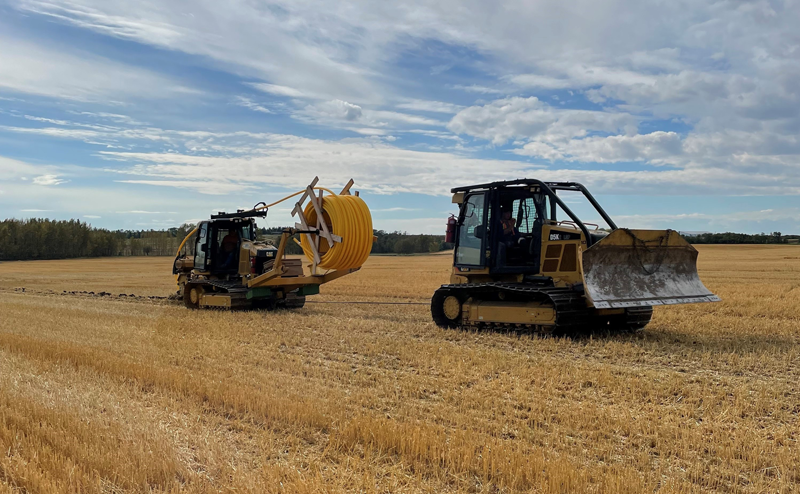
As this evolved, along with continued increases in regulatory requirements and additional reporting, we have increased our Administration staff. This caused cramped workspace for our front office. In 2021 plans were finalized and the expenditure approved to begin construction of a 3400 sq. ft. addition to our office building using utilizing the proceeds from the sale of CCI Wireless. The addition includes a Training Center where we can do much of our training in-house and serve as a meeting room for the Board of Directors. Construction and renovation began in the Spring of 2022 and was completed in Spring 2023.
In 2023, our self-construction statistics grew exponentially. With 36 new services requiring 16 km’s of pipe, legacy pipe upgrades requiring 11 km’s and 13 km’s of looping and re-routed lines, made for a record year totalling 41 km’s of new pipe installed. This allow us to keep up with the increasing demand for gas on our system and expanding membership . Our Meter Station replacement continues as facilities can be procured.
Respectfully,
Board and Management G.L.D.C. Gas Co-op Ltd.